
Right Choice
Why Choose Us Sterikaam Healthcare

Quality Reprocessing & Operational Distinction
Collaborating with Sterikaam secures excellent standard operating protocols (SOPs) that will guarantee safe and reliable sterilization. We manage your sterile reprocessing in accordance with the standards set by the manufacturer.

Inventory Optimization
With our sterile processing solutions, you can maximize your return on investment for surgical instruments (assets) by using end-to-end tracking and monitoring to reduce instrument loss, ensure accountability, and make data driven decisions.

Compliance
Convenience
Many healthcare facilities find it challenging to keep up with changing standards and regulations. With our reprocessing management and optimisation services, we make it simpler for you to acquire and keep the certifications and audits you need.

Internal Transparency
Transparency is critical across the healthcare spectrum. Our open work culture of strong lines of communication between departments makes it easier to streamline OT turnaround time.

Minimizing Risk,
Maximizing Outcome
All our sterilization techniques prioritize patient safety and prevent hospital acquired infections (HAIs) by strictly adhering to minimum touch policy, aseptic arrangement, and infection control standards.

Cost Viability
By implementing our efficient workflow and distribution model, you get to substantially reduce condemnation, repair, maintenance, utility, and manpower costs.
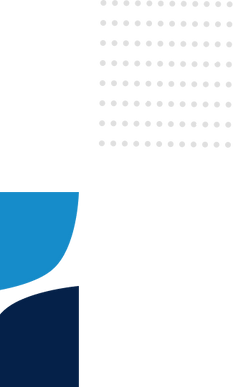


Workflow Layout
Functional workflow of CSSD Layout
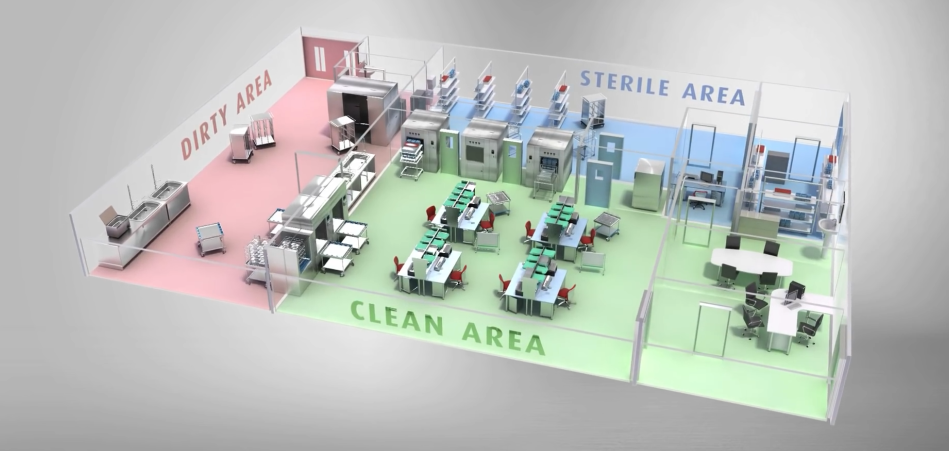
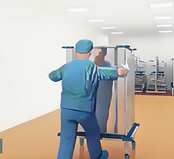

Arrival
-
Designated unsterile trolleys are received at the receiving section.
-
Instruments are verified against the checklist and any damage found is noted and reported to the respective department.


Decontamination
-
Instruments are dismantled & sorted for intensive cleaning.
-
Instruments are pre-rinsed in cold (<43C) RO water to remove any pretreatment products or blood. For specific hollow devices, instruments are manually brushed to remove any dried secretions and excretions.
-
Instruments are then immersed in an enzymatic and anti-rust solution. [Corrosion inhibitors protect surgical tools, sequestrants prevent soil redeposition and spotting on instruments, and chelating agents block & remove scale build-up.] The cleaning detergent is low-foaming, allowing staff to look into the sink clearly to identify all instruments and avoid injuries from sharp objects.
-
Finally, the instruments are rinsed and dried in a thermal drying cabinet or with an air gun.
-
Ultrasonic cleaners are used to remove soil from joints, crevices, lumens, and other inaccessible areas through the process of cavitation and mechanical vibrations. A pass-through window is required to transfer the instruments to the next zone.. It is advisable to use double door washer disinfectors that mechanically process items before automatically unloading them into the clean side. (Flushing, Washing, Rinsing, Lubrication, Thermal Disinfection, and Drying)



Control & Packaging
-
The instruments are inspected for proper functionality and are lubricated at the appropriate joints.
-
Instruments are further assembled into sets and mesh trays along with appropriate indicators. These are wrapped utilizing the OT Kit List’s a double envelope packaging process with aseptic arrangement in an SMS or linen packing.



Sterilization
-
Autoclave: Instrument sets are loaded into a three-phase autoclave (Pre-conditioning/ Pulsation, Exposure, and Exhaust) - 134C/3.5 min
-
ETO: Equipment such as Ambu bags, tubings, cannulas, guide wires, electric circuits, sheaths, octopus, laparoscopic instruments, and so on, cannot be sterilized at high temperatures and hence are sterilized at low temperatures. ETO has a cycle length of 12 to 16 hours and consists of 5 phases (Preconditioning, Humidification, Gas introduction, Exposure, Evacuation, and air washes).


Store & Dispatch
-
A double-door sterilizer acts as a barrier between the clean zone and the sterile storage zone.
-
Once the sterilization process is complete, the instruments are unloaded and stored in a dust-free, dry, and cool area and are further dispatched in FIFO order.
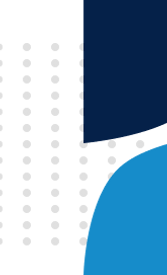
Contact Us
Send Enquiry Message
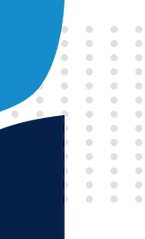


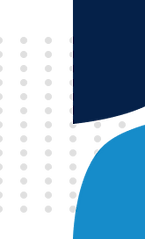